

Does the gauge have the right measurement resolution?.
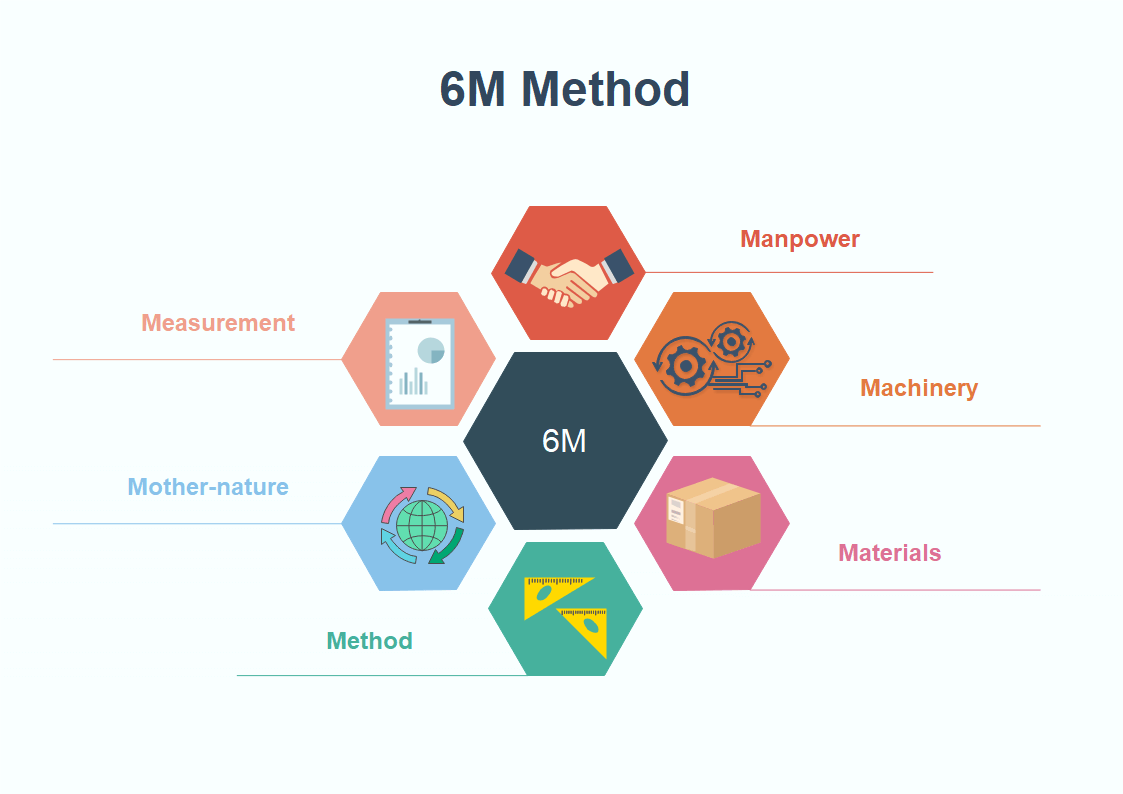
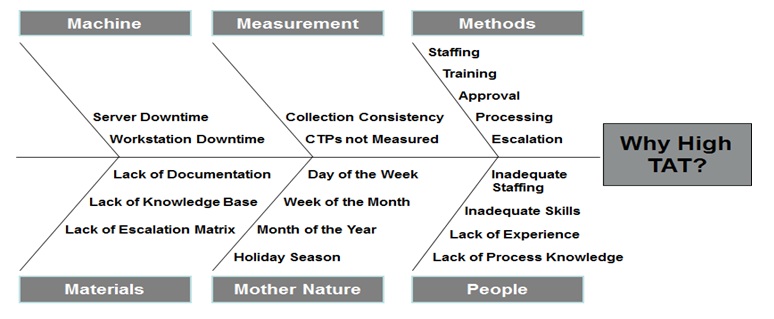
#Ishikawa diagram 6m sample software
Do equipment and software have capabilities that meet the needs of use?.Do software and hardware need to be update?.Is the equipment getting proper care (daily / weekly / monthly maintenance)?.Is the equipment affect by environmental conditions?.Is the file save with the correct extension in the right place?.Does the machine meet the process capability?.Is the machine use exactly to the needs of production?.How much experience does the employee have in performing specific tasks?.Are employees accountable and reliable enough?.Is the work efficiency of the employees acceptable?.Are there issues related to worker fatigue?.Are there any disruptions occurring in the work area?.Does the environment affect individual work activities?.Are guidelines for making those assessments available?.Is there too much assessment to do before starting work?.Has there been enough training for employees?.Did the recipient of the information have understood the messages convey?.Has the information been properly channel to all functions in the process?.Are the existing documents comprehensively understood?.Questions to Ask When Creating Fishbone / Ishikawa Diagram Two additional causes in manufacturing are: Management / Money Power, and Maintenance.įishbone Diagram 7P Concept for the Marketing Industry:įishbone Diagram 5S Concept for Service and Service Industry: Some of the concepts taught stick to a simple and easy-to-understand system do not use the term 8M. But the concept of 8M is not widely known. The concept of 6M has been develop in such a way as to form the 8M formation. The Fishbone diagram uses the 6M concept originally use in the Toyota Production System (TPS). Man-power (physical workers) and Mind-power (non-physical workers).Materials (including raw materials, consumables and information).To identify the causal factor can use root-cause analysis or 5 Whys (why why analysis) method. The categories that appear can be some of the above mention, as well as something else. This Ishikawa diagram can reveal the relationships among variables that are diverse, and those causal factors will present additional facts about the process behavior.Ĭausal factors can be obtain by brainstorming. The causal factors in Ishikawa diagram or fishbone diagram are categorize and known as 6M. Environment: environmental conditions such as location, time, temperature, and culture where the process operates.Measurements: data taken from the process use to evaluate the quality of the process.Material: raw material, part, paper, pen, etc.
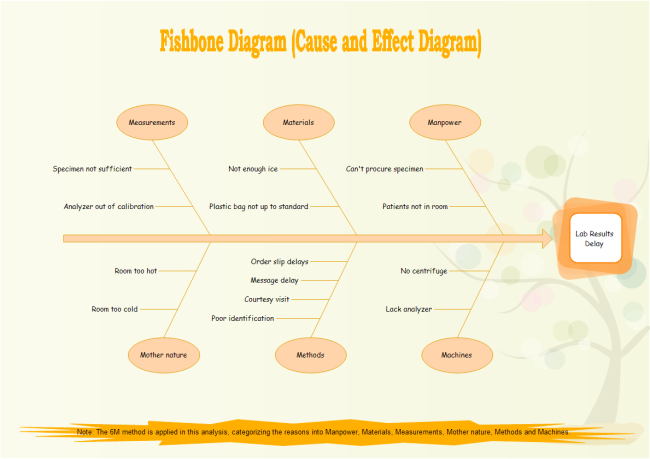
Machines: equipment, equipment, computers, tools, etc., need to do the work.Method: how the process runs and some things to watch out for before the process goes, such as policies, procedures, rules, regulations and laws.The causes are usually group into main categories to identify the sources of those variations. Every cause of imperfection is the source of variation. Ishikawa diagrams are use in the planning of a product to prevent the occurrence of defects or degradation of quality, by identifying potential causes of defects that cause certain effects. The Fishbone diagram or also known as Ishikawa diagram is a causal diagram created by Kaoru Ishikawa (1968) which shows the causes of specific events.
